Matt Raynor is stressed. The 53-year-old chair of Raynor Foods has recently approved a £1,200 signing-on bonus for sandwich makers; tonight he will work a six-hour picking and packing shift at the company’s Essex plant because of staff shortages.
“It’s been the worst two-and-a-half years of my life, with the disruption, the chaos,” he says. “We were fighting with Brexit and then Covid hit us.”
Raynor’s family business, founded in 1988, makes 80,000 sandwiches a day for cafés, supermarkets, canteens and hospitals. Once a makeshift operation in his parents’ kitchen, its rise has mirrored the professionalisation of the UK’s sandwich industry over three decades.
Since the 1980s, a large chunk of British sandwich making has moved from kitchens and sandwich bars to chilled, hyper-efficient factories, which produce a wide variety of packaged sandwiches — from the humdrum cheese and pickle to novelty flavours involving jackfruit and plant proteins. The industry’s rapid growth was powered by rising incomes, more women joining the workforce, cheap labour from Europe and workers chasing convenience.
Now, after the pandemic dealt the industry the worst blow in its modern history, it is being reshaped by a combination of labour shortages, souring economic conditions and changes in British working habits.
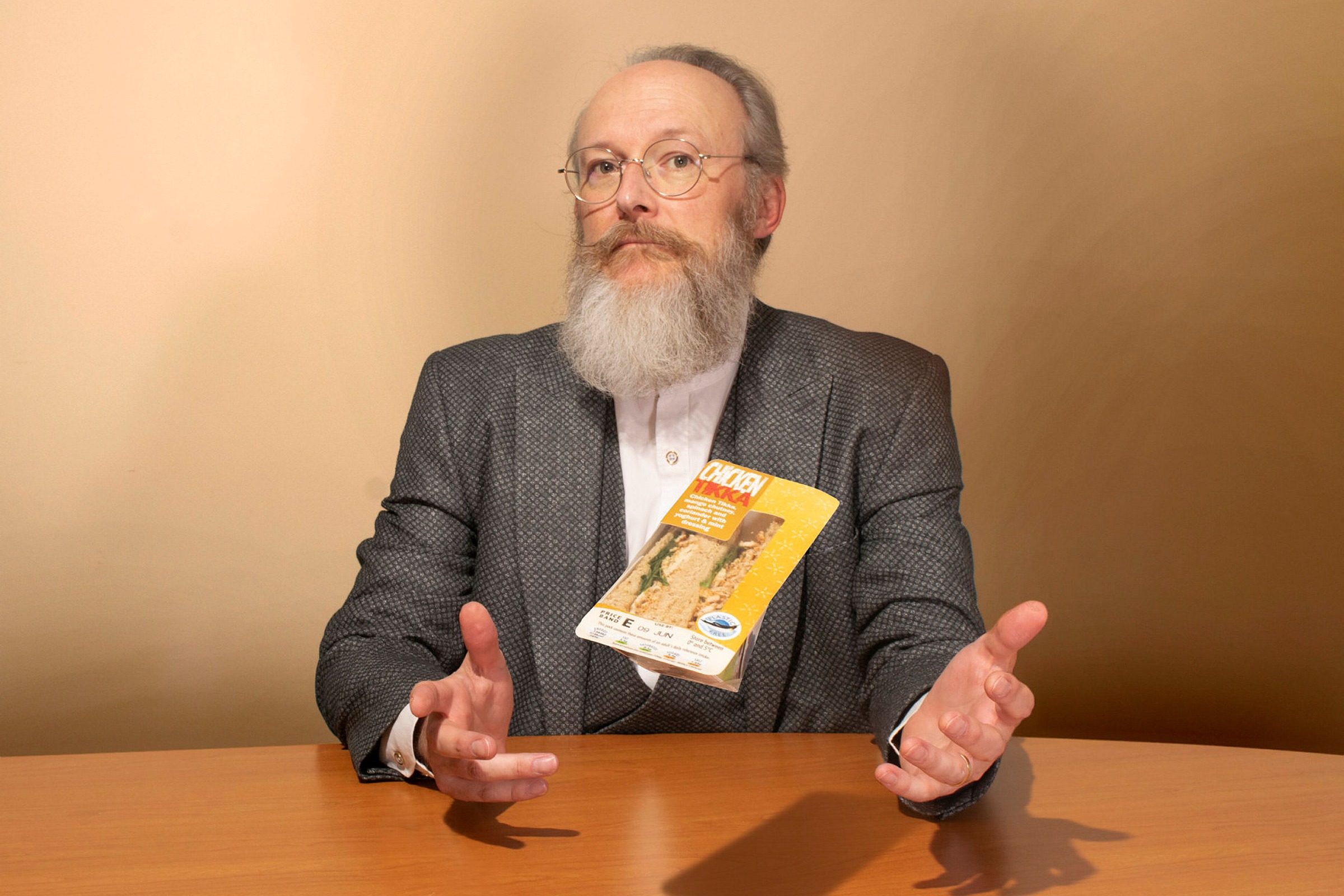
Chairman Matt Raynor’s parents founded Raynor Foods in 1988, and it now supplies 80,000 sandwiches a day
Raynor Foods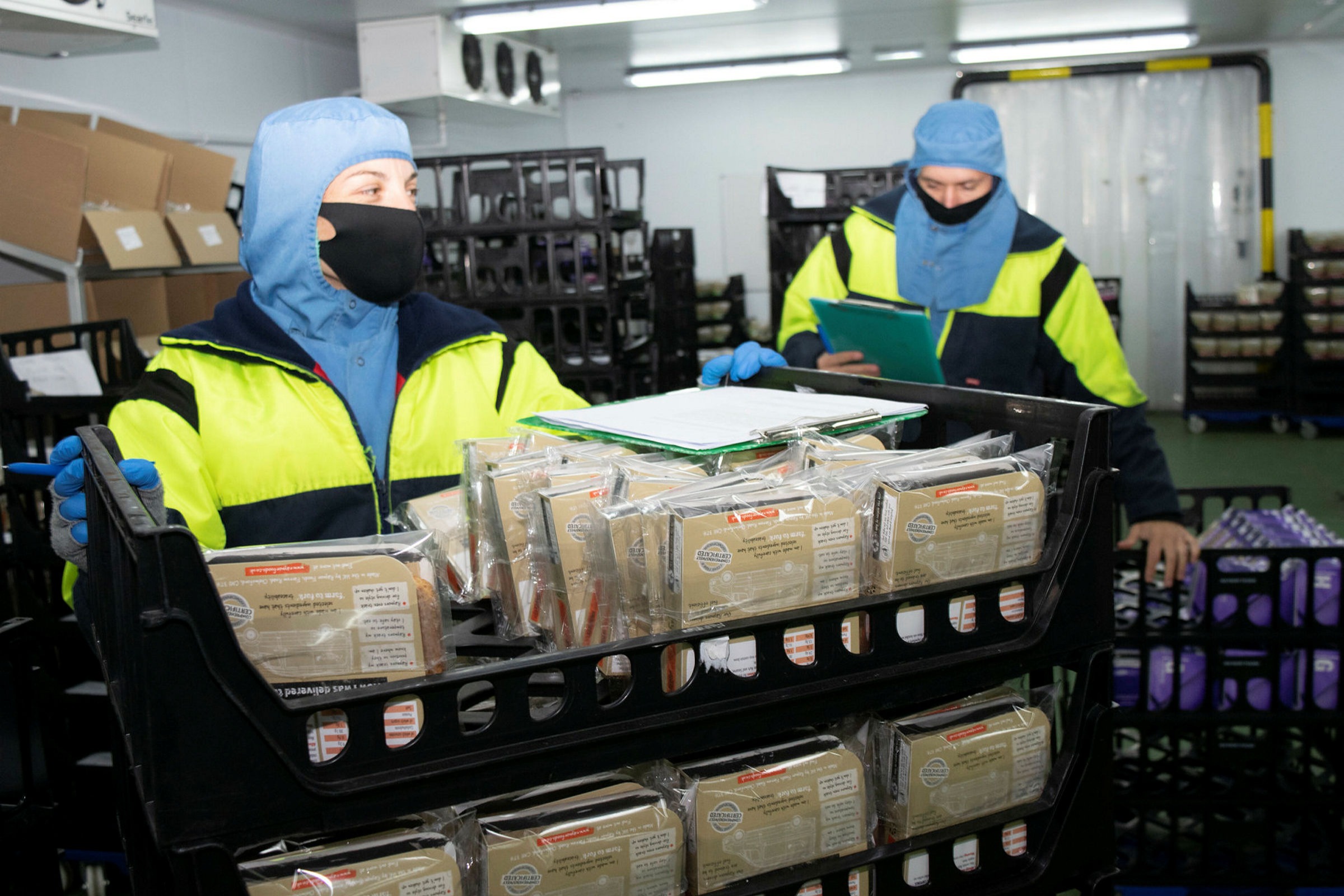
Staff at Raynor Foods work for long periods of time in cold rooms
Raynor FoodsBefore Covid lockdowns temporarily shuttered offices in 2020, people in the UK were eating £8bn worth of sandwiches a year. Kevin Moore, deputy chief executive of the UK’s largest sandwich maker Greencore, says packaged sandwiches had reached a so-called penetration of 84 per cent — meaning 84 out of 100 people bought at least one a year, a rate exceeded only by a few staples like milk and coffee, according to Kantar, a data analytics company.
But the rise of homeworking during the pandemic seems to have driven lasting changes in the routines of the industry’s most important customers: office workers. The British Sandwich & Food to Go Association estimates that, two years on, business is still 20 per cent below pre-pandemic levels.
At the same time, the sector is facing disruption to its supply of cheap labour and ingredients. Brexit closed the UK’s doors to free movement of EU citizens, meaning production workers are scarce and their wages are rapidly rising. Intense inflationary pressure is adding to the unpredictability of purchasing and supply chain hold-ups since Russia invaded Ukraine this year.
“I’m concerned for the whole industry,” says Raynor.
Just in time
While the sandwich is not about to vanish from British culinary life, the industry fears its pre-pandemic golden age, marked by low cost and seemingly infinite variety, may never return.
When Raynor’s parents moved from running a restaurant to making sandwiches 34 years ago “there was no sandwich industry”, he recalls. His father met the buyer for a group of Co-Op stores at a networking event, who said they needed a sandwich supplier. The kitchen operation began.
“It took us nine and a half hours to make 350 sandwiches . . . we had to grill the bacon and boil the eggs, do everything from scratch,” Raynor says. “They were beautiful sandwiches,” he adds wistfully.
Today, making sandwiches is a precision business requiring frenetic backstage activity. At Pret A Manger, the sandwich chain that has become synonymous with London commuting life over more than three decades, sandwich-making starts in-store at 5am each day. Elsewhere, production lines work frantically during evenings and nights.
At the south London plant of Simply Lunch, a manufacturer with 290 staff, making a bacon, lettuce and tomato sandwich requires 17 stations on the production line. The orders — between 400,000 and 450,000 of them each week — come in just 48 hours before the sandwiches need to be on shelves.

Workers in protective gear operate in rooms where the temperature hovers at around 2C, processing 25,000 loaves of bread a week and two tonnes of tomatoes. Fifteen people are dedicated to food safety. The facility operates 20 hours a day, with the remaining four spent on cleaning. Hermann Dokoui, a shift manager at the plant, says the 9pm to 7am night shift is the hardest “because you are always walking around”, preparing for deliveries to leave the factory.
The need for freshness means sandwiches cannot be made overseas. “The sandwich industry has transformed short shelf-life, chilled distribution in the UK dramatically,” says Jim Winship, director at the BSA. “You have production plus two days or three at most. That means they’ve got to get from the factory, which might be in the Midlands, to the retail shop, which might be in Inverness somewhere, and sell it within two days.”
Simply Lunch’s lettuce leaves are picked in Kent in the small hours, reach the factory at 9am, pass through a sanitising chemical solution, spin in a giant salad spinner and are inside sandwiches from noon. Ultrasonic blades cut the bread. Finished sandwiches are weighed to check the protein allocation. Samples go to laboratories daily to check for bacterial contamination.
When a production line changes from one product to another, the procedure resembles a “Formula One pit stop”, says Sam Page, Simply Lunch managing director. “There is a lot of technical knowledge that goes into a sandwich.”
That precision has been tested by a dwindling supply of labour since Brexit. Page’s factory has around 40 vacancies. Another headache is the sheer pace of inflation. This year egg prices have risen by 30 per cent, mayonnaise by 80 per cent as vegetable oil prices spiked, and bread prices by 25 per cent, says Adam Newland, managing director at Raynor Foods. Now the headache is cheese, where prices have risen 76 per cent in a year to £6 a kilo.

“There are forecasts that it will be going for £8 a kilo by year-end. Cheese is still incredibly volatile,” Newland said. Despite some commodity prices going into reverse, “nothing has eased for us,” he says.
Ingredient shortages caused by supply chain disruption are forcing manufacturers to adapt constantly, says Winship. Most have cut their ranges to streamline production. Greencore reduced its number of products by one-quarter after the onset of Covid-19 and it remains about a fifth below pre-pandemic levels. Simply Lunch cut its offering from 150 items to 100.
Government support enabled most sandwich makers to survive the pandemic, but Southall-based Adelie Foods entered administration in 2020 with the loss of 2,000 jobs. Now Winship estimates the industry is operating at about 80 per cent of pre-pandemic sales, or £6.4bn a year.
He had hoped for a full bounceback in 2022, but after the onset of rapid inflation this year, he is not so sure.
Follow the skyscraper
The success of the British sandwich industry over the past four decades belies both the precariousness of its business model and the intensity of the competition between manufacturers. Margins are inevitably tight when speed and convenience are king.
Marks and Spencer introduced its first packaged sandwich — salmon and tomato — in 1980. Pret A Manger was founded in its current form in 1986. Greencore emerged from the 1991 privatisation of Irish Sugar.
The broader national climate favoured sandwiches. British prime minister Margaret Thatcher’s labour reforms of the 1980s provided sandwich makers with “relatively low-paid workers”, says David Edgerton, professor of modern British history at King's College London. The white-collar ethos became one of “people working harder, with not much time”.
As food writer Bee Wilson notes in her book Sandwich: A Global History: “No dish has a stronger association with the world of work.” For employees without a subsidised workplace canteen, sandwiches became a cheap, efficient way of outsourcing lunch. “Instead of communal eating, it [became] a solitary activity,” says Edgerton.
Today, in real terms, average household disposable income is double that of 1980, says Jon Boys, economist at the Chartered Institute of Personnel and Development. “Extra income means more stuff. Tasks like making sandwiches have switched from home production to the market economy — as have many other things over the years: childcare, cleaning, shopping.”

Oriel Sullivan, professor of sociology of gender at University College London, says the 1980s were when “female full-time employment rates really started to rise rapidly. There were fewer women at home to make sandwiches for others, and they were too busy to make them for themselves.”
The ready-made sandwich became emblematic of the era’s economic shifts. Boys says: “What are you buying? A sandwich, yes, but really you are buying time, convenience, consistency and perhaps variety too.” The brand that summed up that change was Pret A Manger, whose previous chief executive’s motto was to “follow the skyscraper”.
With few barriers to entry for manufacturers, the market soon became intensely competitive. “Retailers have moved their contracts around and kept margins low,” says Andy Searle, managing director at consultancy AlixPartners.
A ready supply of cheap and pliable labour enabled that strategy. After the EU expanded in 2004, many vacancies were filled by eastern Europeans who were willing to work long hours for lower pay. By 2017, EU nationals accounted for more than one-third of the food industry workforce, according to the Food and Drink Federation. They were disproportionately working on production lines, say industry executives.
When it came, Brexit was accompanied by an offer of long-term settlement for existing European residents. But a points-based immigration regime introduced from 2021 stopped the free flow of low-paid labour, while the Covid pandemic prompted an estimated 1.3m overseas workers to head home.
That led to an intensive recruitment drive. Pret, Greggs and other takeaway chains have suffered staff shortages after making redundancies or furloughing workers during lockdowns. Pret, which increased headcount by 28 per cent between January and April this year, has raised wages twice since September. Sandwich executives say Amazon warehouses can easily poach their employees.
With post-Brexit immigration policy shaped around a “high-wage economy”, ministers have pushed food manufacturers to automate rather than employ low-paid workers. But it is a major challenge to replace the dexterity of human fingers when handling irregular ingredients such as lettuce.
Simply Lunch is investing £25,000 in a “depositor” to drop egg mayonnaise or a similar mix on to bread. Another robot drops the final slice of bread to “lid” a sandwich. Greencore already uses both devices, along with a butter spreader.
Raynor Foods has a robotics programme with Dutch group IRS, but it has yet to juggle multiple ingredients — a task Raynor compares with Tetris, the video game. His company has been battling vacancies and staff turnover despite raising entry-level wages by 15 per cent in a year and ramping up bonuses. Of one group of 17 new recruits, four dropped out within two days.
“We are asking people to do a physical job in a cold room without any windows, for long periods of time,” he says, adding wryly: “The glamour of the industry is not at the coal face.”

End of the cheap food era
The greater challenge may be getting consumers to return to their pre-pandemic lunching habits. Food perks are one way to entice staff back into the office but, for many, a sandwich will not cut it, says Julie Ennis, chief executive of UK and Ireland corporate services at caterer Sodexo: “People are looking for something different . . . People aren’t coming into the office for a ham sandwich,” she says.
Food delivery apps have increased consumers’ expectations of choice. Matt Ephgrave, managing director at Just Eat for Business, says the past six months have prompted “unprecedented demand” for food deliveries to offices. “We’re seeing a massive shift towards healthy options — Japanese, Poke bowls and salads,” he says.
And in recent months, some of the major economic trends that helped fuel the sandwich boom have gone into reverse. The Bank of England has warned of the worst squeeze on disposable incomes in 30 years. The resulting cost of living crisis is expected to have far-reaching effects on British lifestyles.
Some manufacturers are handling the price pressure by quietly cutting portion sizes, says Andrew Walker, former chief executive of sandwich chain Eat. Raynor has pushed up prices for its customers by as much as a quarter.
“The evidence is that the era of cheap food is over,” says Tim Lang, emeritus professor of food policy at City University. For Lang, sandwich manufacture is a carbon-intensive industry, over-reliant on cheap labour. “You’ve got a plastic-wrapped sandwich made overnight in a factory up the A1 and driven down in cold store, oil-guzzling trucks to deliver to put in a BP M&S garage. Is it sensible? It’s bonkers,” he says.

Walker believes the heyday of the traditional triangle sandwich is over, but for a different reason. He argues it will decline as consumers choose salads, wraps and other options that are seen as healthier.
Others are more optimistic. “The core of this nation is run by . . . blue-collar workers in manufacturing. They need a sandwich on the go, they don’t have time to have dinner and they love what they love,” says Dan Silverston, managing director of The Soho Sandwich Co.
Some remote workers may be convinced to buy their packaged sandwiches close to home. Sales in Pret’s suburban London shops are now 18 per cent higher than pre-Covid levels while City stores’ sales are still around 17 per cent lower, Bloomberg data show. The motto of its current chief executive, Pano Christou, is “take Pret to the people”. But, Xiaowei Xu, senior research economist at the Institute for Fiscal Studies, expects this trend will make sandwiches more expensive “because places where people live are less dense than places where they work”.
As for Raynor, he argues the sandwich will be “dragged kicking and screaming back to pre-Covid levels of variety, but that will be massively stymied by inflation . . . It will take time and customers will have to accept that the price for a sandwich will not be what it was two years ago.
“Nothing else is going to stand still,” he says, “so why would the sandwich?”